Eagle Prep
I redesigned the software Digital Control Inc. uses to manufacture its latest product line through its Manufacturing, Quality Control, Configuration, and Repair departments. Each of these departments have a coordinated role to play when a product is built. My goal was to create software that allowed each department to do their job on each device efficiently, clearly, and with few errors (if any).

My Role & Responsibilities
-
Interview and observe employees of each department
-
Create personas of the end-users for each department
-
Create and iterate on workflows, wire frames, sketches, and prototypes
-
Create low to high fidelity prototypes and perform usability testing with each department
-
Work with visual designers to bring the new design to life
-
Create comprehensive design specifications for software developers
Where It All Began
The original manufacturing software used to setup devices was internally designed and created by software developers. The software did its job but did not have any workflow, and departments were unsure what their responsibility was within the software. The main menu was a long list of different functions each with their own utility with no connection to any others.

Research & Results
I first conducted interviews of managers and employees of each department involved. I asked about how they currently work, what helps them succeed, and what their worries and fears are with the manufacturing process. I then conducted a full day observation for one employee in each department. I found some interesting results that helped change how I thought of the application:
1
Assemblers manufacture product at least 5 at a time, so repeated actions will be repeated many times. Automation is important to increase efficiency.
3
In the past when steps and responsibilities are not clear. Errors and additional training was the result.
2
Most departments use bar code scanners as the primary device for inputting data and the keyboard is rarely used. The interface must be optimized for scanning.
4
Quality Control and Repair departments are frustrated with products made to work, but not to be tested or repaired.
Understanding and Creating a Workflow
Grouping exercises were employed to better understand each department's responsibilities and flow with the software. They used sticky notes to show what features they used and then connected those features to others that were used in sequence. From there we started to put together a flow for each department.
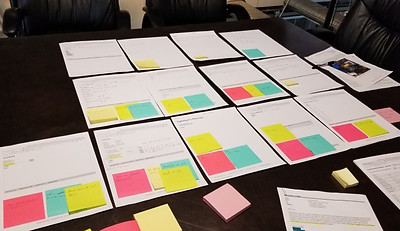

After talking to each department, a company workflow emerged that would work well for the software…

Prototyping and Iteration
Prototyping first started in paper form and gradually worked its way up to low-fidelity then high-fidelity prototypes with each iteration. I used Sketch to create the software screens, then InVision to turn them in to functional prototypes. Usability testing was done for each iteration to test for efficiency, understanding, and the amount of errors.
There was a focus to make each step of the manufacturing step clear using automation where we can. No more having to click on each individual action in sequence and remember the order to click on them.
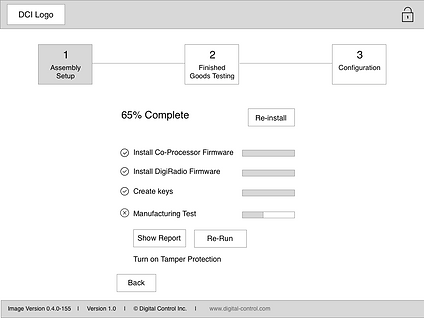
It was important to support and optimize for bar code scanning on every input screen. Immediate feedback was provided on scans. The user was also able to automatically advance to the next field without needing to use the mouse or keyboard. This added up to major increases of efficiency in data entry.

The Final Product
I worked with a team of Visual Designers and Software Developers to create the final solution based on the User-Centered Design process. The result was a solution that exceeded usability requirements and was an experience that improved productivity for all departments involved.

